In the fast-paced world of technology, power banks have emerged as lifesavers for our devices. But how exactly are these essential gadgets made? Join us on a detailed journey through the power bank manufacturing process, ensuring you understand every step of the way.
Table of Contents
ToggleRigorous Quality Control: Setting High Standards
Before diving into the assembly, our Incoming Quality Control (IQC) team plays a pivotal role. They inspect every component that arrives:
1.1 A thorough 100% appearance inspection of all raw materials, ensuring no defects.
1.2 Random PCB samples are selected and tested for functions like internal impedance.
1.3 Cell samples are chosen at random to verify their real capacity.
1.4 Cable samples are also randomly picked and checked for functionality.
To give you an idea of our stringent standards: out of a batch of 3,000 to 10,000 PCBs/cells/cables, we select 300 for inspection. If more than 3 units are found defective, the entire batch is returned to the supplier, adhering to the AQL standard used by industry leaders like Xiaomi.
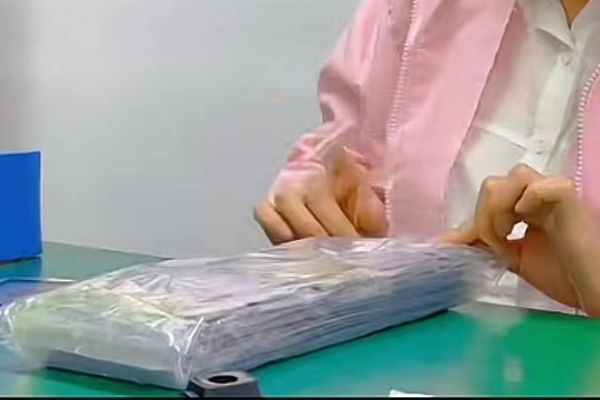
Assembly: Crafting the Powerhouse
The assembly line is where individual components come together to form the power bank:
2.1 PCB boards are prepared and wires are soldered to connect to batteries.
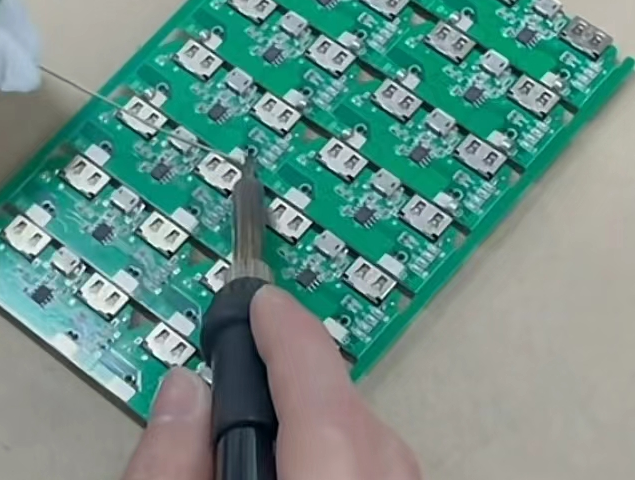
2.2 Lithium polymer cells are readied and safeguarded against potential short circuits.
2.3 To ensure stability, spongy material is added to the cell, preventing any internal movement.
2.4 Cells are connected to the PCBs, and each unit is tested for both charging and discharging.
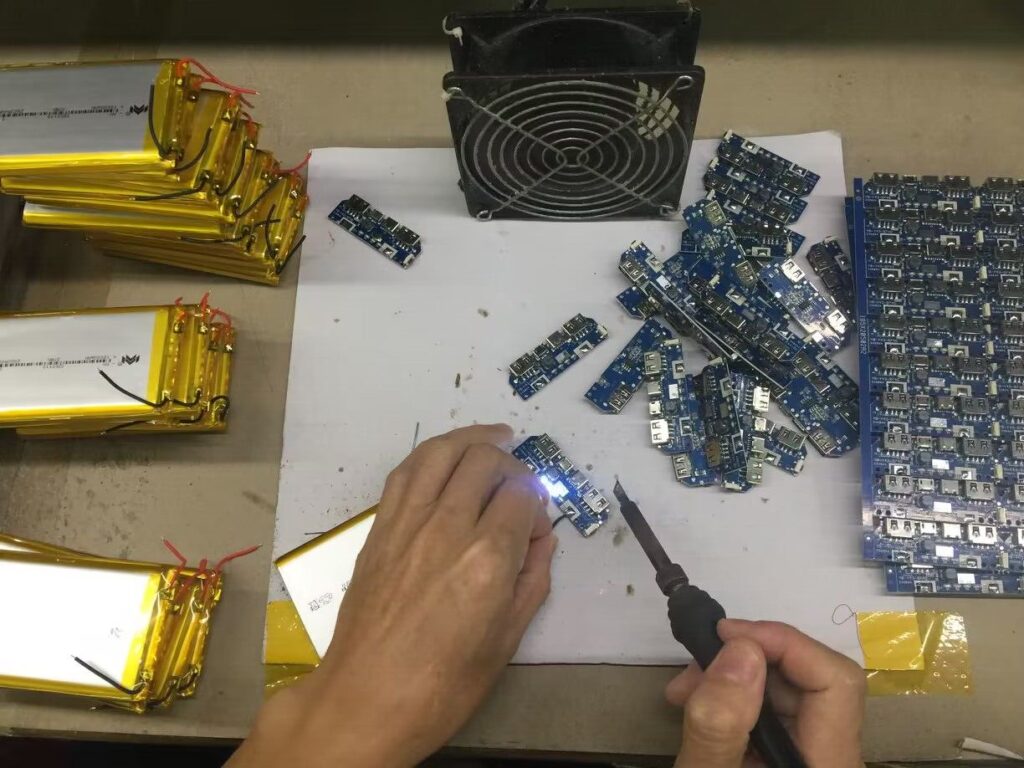
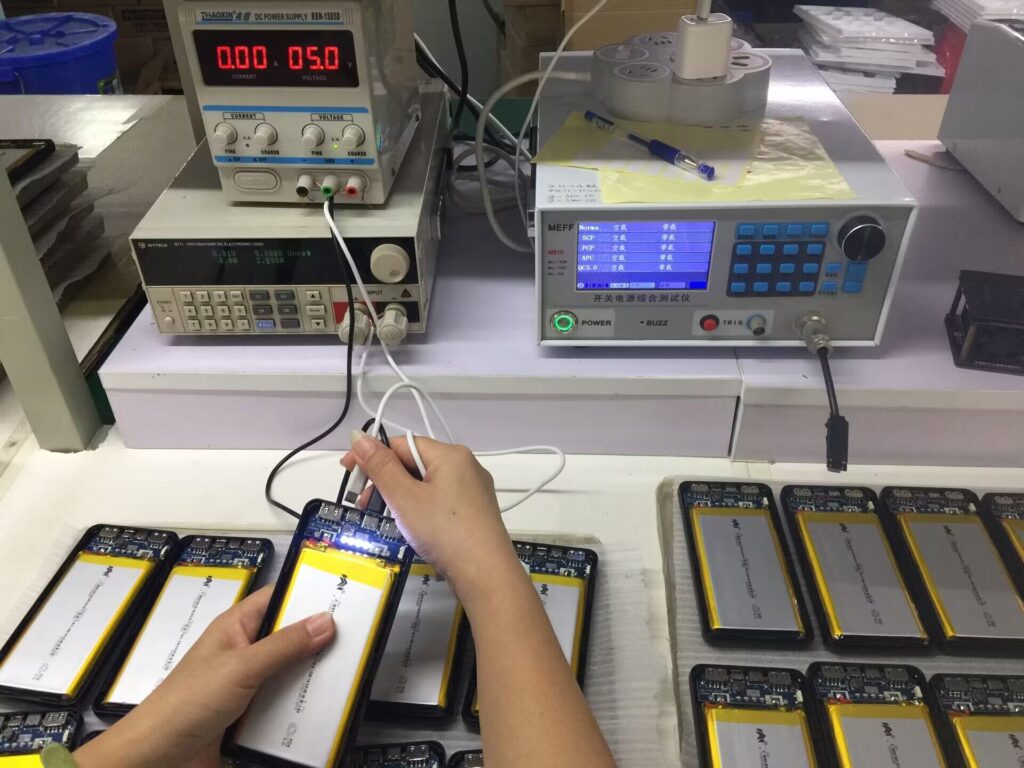
Personal Touch: Adding Your Custom Logo
To make each power bank unique, we offer the option of imprinting a custom logo. Using state-of-the-art techniques, your brand’s logo is seamlessly integrated into the power bank, ensuring it stands out in the crowd.
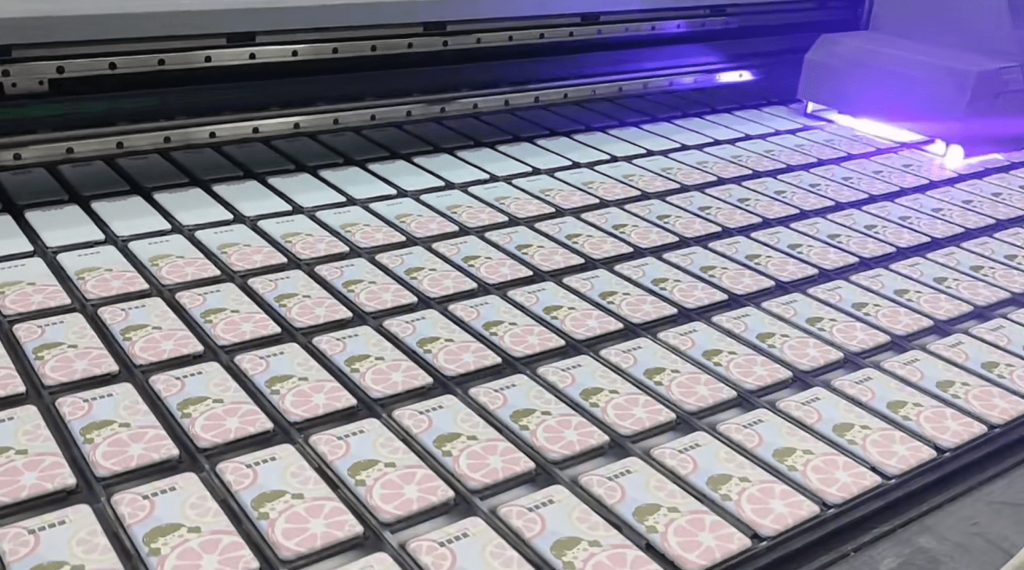
Aging Testing: Guaranteeing Reliability
Each power bank undergoes an aging test, where it’s charged and discharged in a cycle. This step, often skipped by others to save costs, ensures the longevity and reliability of our product.
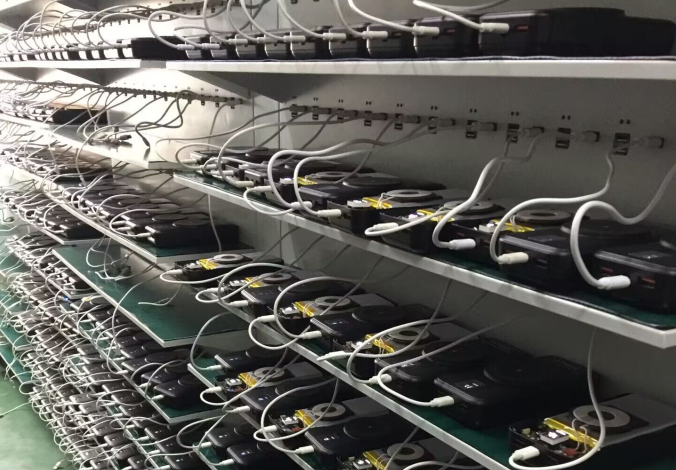
Final Checks & Packaging: Ready for the World
As we near the end:
5.1 The power bank is sealed securely.
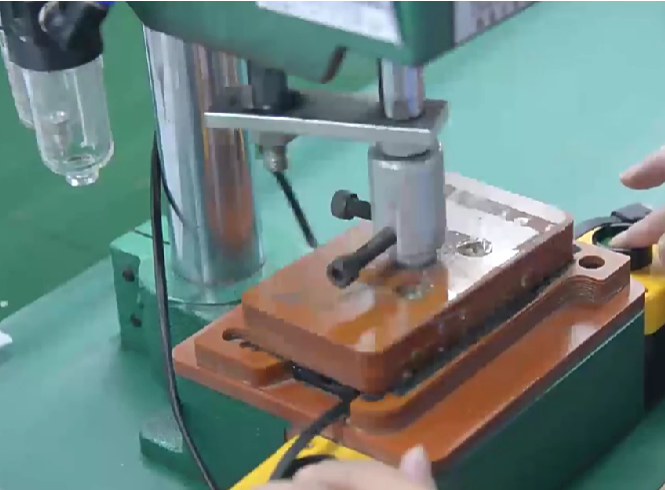
5.2 It undergoes another round of functionality tests.
5.3 Once approved, it’s cleaned and prepped for packaging, where it’s presented in a manner befitting its quality.
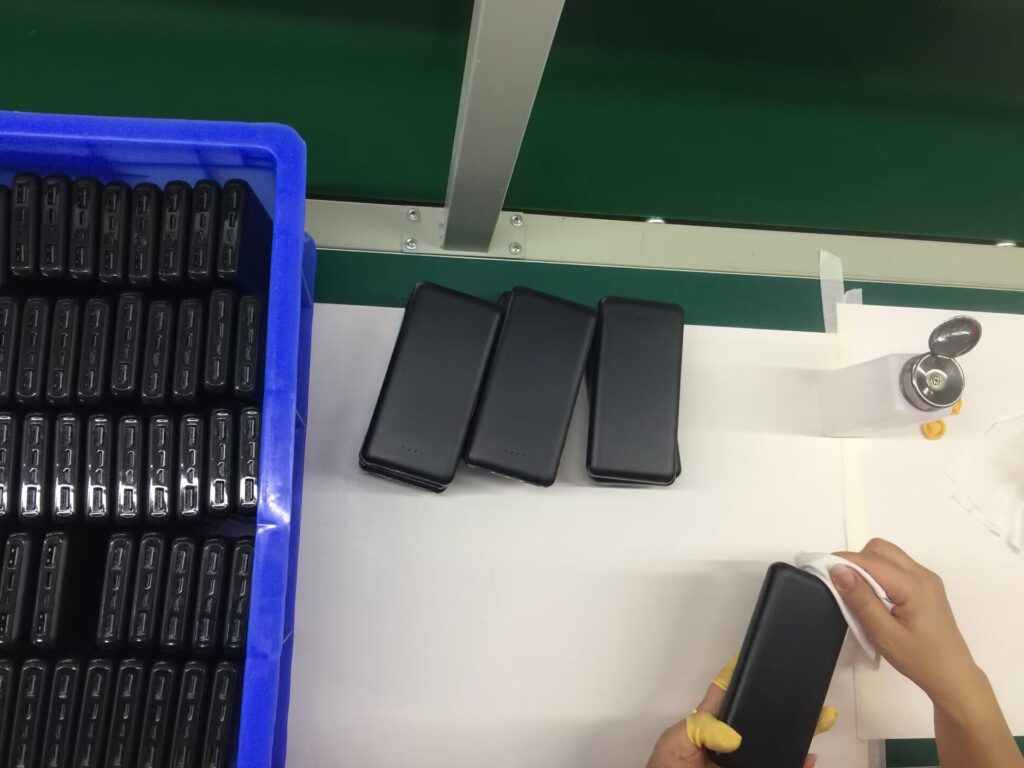
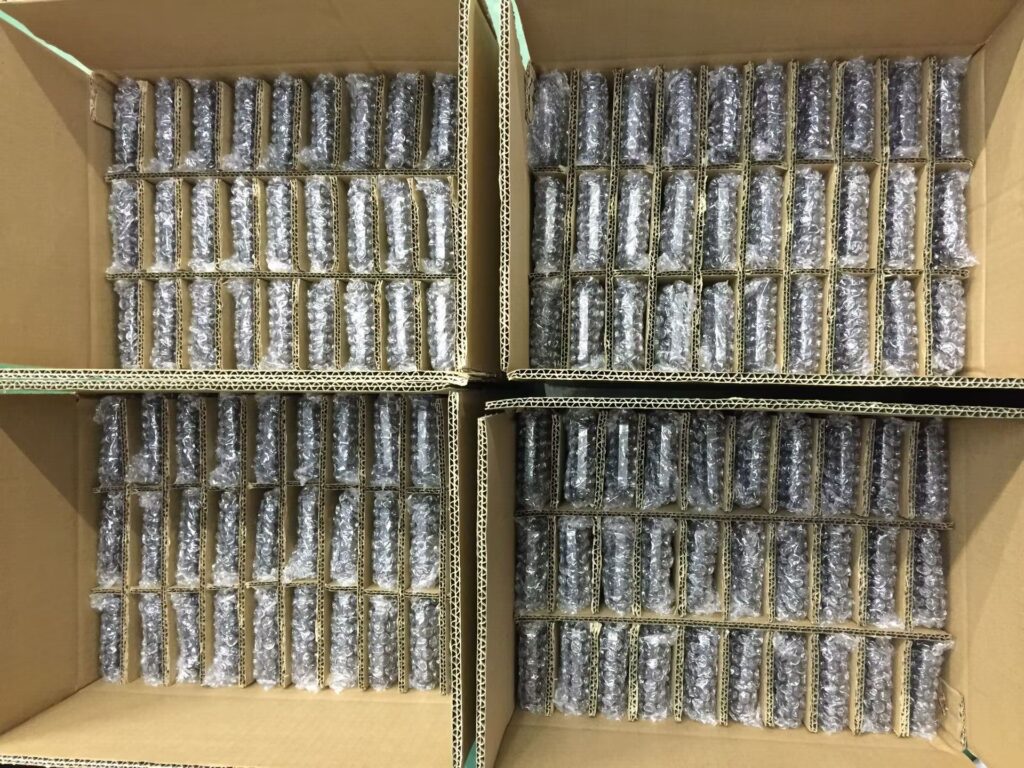
Conclusion: Power Banks, Demystified
From rigorous quality checks to the final packaging, now you’ve seen the meticulous process behind crafting a power bank. Whether you’re a tech enthusiast or just curious, we hope this guide shed light on the journey of a power bank from raw materials to your pocket.